Capabilities
Introduction into G-TEM Capabilities
G-TEM possesses a full complement of capabilities in order to achieve OEM requirements from large in-house cast die manufacturing, material procurement, world class production capabilities via fully automated large AIDA stamping process and complex automated multi robot assembly lines for Ultra high strength steel, Aluminium & steel.
Stamping
- Hybrid capability – UHSS / Aluminum / Steel
- x9 – Fully Auto high speed AIDA Transfer lines (1920 Width * 6mm Material Thickness)
- x5 – Large Automated AIDA Progression lines (2000 Width * 6mm Material Thickness)
- x10 – Automated Progression lines with Profile blank capability
- Automated closed loop scrap reclaim facility.
- x5 Try out Presses ranging from 500 ~ 1000 Ton







Assembly
- Fully automated complex assembly lines
- Automated stamp nut capability (Profil & SPAC)
- Automated SPR technology
- Spot & Projection
- Laser Welding
- Friction Stir Welding
- Bonding
- Various NVH applications
Wireforming
- Highly flexible wire bending / spring forming solution using 6-axis CNC Wire Formers.
- Ability to form wire in a vast range of OD’s. (3~ 14mm)
- Cold Forming heading operations.
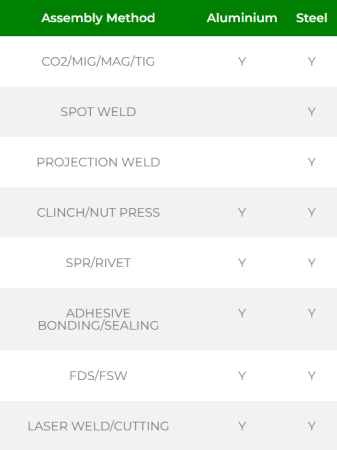







Quality
IATF 16949 & ISO 9001 Accredited
JLR Q Award from Jaguar Land Rover
Best Class Quality Achievement with 4 Major OEM's
Q&D Awards from Multiple Customers
- Fully equipped Metrology centre
- Automated CMM measurement systems
- 3D laser & White light scanning capability
- In-house Material testing capability
- Macro testing facility
- Established audit system
- Full tear down facility

Logistics & Material Management
Logistics
- Fully integrated automotive ERP system interfacing with customers via automotive standards
- Side & rear vehicle loading with 20 minute turnaround time
- Full Automated storage and retrieval system
- Extensive warehousing facilities
- Fully compliant lot control management
- JIT Sequenced supply for complex assemblies
- Small parts Kanban consolidation
Material Management
- Fully automated lot control management for material
- Wide ranging supply base across UK , EU & Asia – both Service centers and mill direct.
- Blank – Via profile , sq shear, Laser.
- Ability to take Mill direct coil up to 20 ton







Die Manufacturing
- X4 Large 5 axis NC Machining Centres
- X6 Small / Medium NC
- Wire Cutting and EDM
- Large conventional machine shop & bench workers
- In House Die design at G-TEM – Allows full Process Planning
- Spotting presses for Die try out
- Grinding facility
- Full gantry cranes across all press areas of production
- Full CAD/ CAM linkage across all NC machines






Procurement
We Can Procure:
- Fasteners
- Fixings
- Tubular Components
- Aluminium Extrusions
- Material
- Machinery
Any requirement you may have we can deliver via global procurement links into multiple regions across the globe.
Our established linkages provide prompt response and quality.




Design, CAE, Simulation
- G-TEM receives data , interrogates, disseminates then carries out full FCR analysis with cost optimization / process efficiency and manufacturability as key points and delivers re-worked CAD back to engineer as simultaneous engineer service with manufacturing capability embedded.
- Full Formability & Simulation reporting
- Full Automotive complaint software

Prototyping & Low Volume
New Investment
- G-TEM has a commitment to ensuring all relevant technological advancements within our sector as well as emerging markets are fully assessed and deployable should a customer need support in this particular area of the supply web.
- EV products are certainly an area G-TEM has focused on and has developed a technology partnership with Fuji Springs in Japan for Primatic battery case manufacture.
- New state-of-the-art E-Coat in-house line is set for system up in 2024 as we see a trend for this within battery area.
- X2 1MWp Solar farms installed at Gloucester facilities in 2022 to support our net-zero targets.
- A further 2MW expansion at original Gloucester facility completed in 2023, bringing total capacity to 4MW across both Gloucester sites.


